Yacht Construction & Refitting
Project Management
Portrush oversees yacht construction and refitting projects, providing leadership and management over trades, design, contracts, budgets, schedules and operation.
- Vessel Construction
- Engineering Design
- All Vessel Systems
Owner’s Representative
We fulfill all necessary duties on behalf of the vessel’s owner to make sure the highest quality work is delivered at the best price and timeframe.
Quality Assurance
Good Quality Assurance is a tool enabling the builder to build to a correct standard and ensure that the standard is followed through to his staff. Portrush will monitor and control all aspects of construction in accordance with the best international QA standards and procedures.
Quality Control
Every project has a clear and concise Quality Control method to ensure that the quality of the build is set to maximum. Good Quality Control is essential to keep all involved in the build to ensure that the end product is built to the best quality they can achieve.
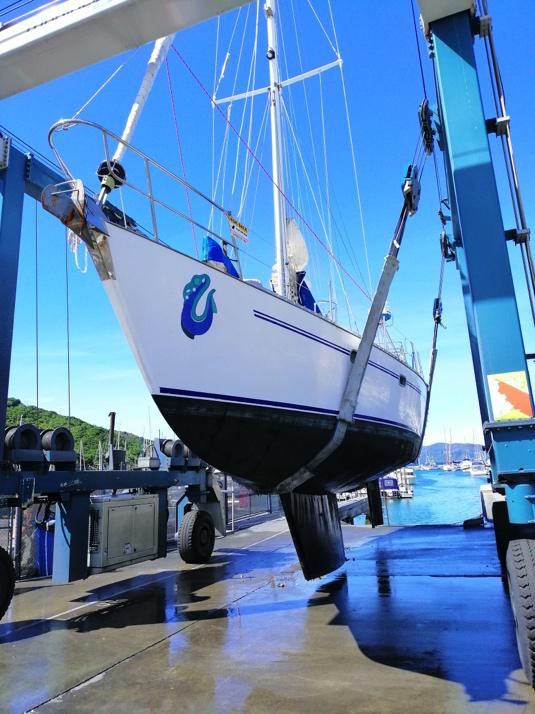
When Quality Standards Aren't Followed
The sales team of a yacht construction company sold a client his dream boat, a 75 foot cruiser. The owner and his family happily received their new 2.5m dollar yacht at Christmas. On their first cruise unfortunately it hit rocks off the North Island of New Zealand.
After our team salvaged the vessel, a very concerning and detrimental picture began to take shape.
How building without Quality Control and Quality Assurance cost a yacht owner over $250,000 in repairs
This is a short brief of the problems, issues and challenges we were faced with in this real case of a $2.5 million cruiser built outside of New Zealand in a region where international standards for yacht construction are not stringently applied.
Drive train damage
A very small 1⁄2’stainless steel bolt was all that was holding the entire drive chain which was being supplied with two 705 H.P Diesel engines.
And in just 200 hours of running, all the drive chain bearings including the seal head received irreparable damage due to the entire drive chain alignment.
Incorrect fittings
Completely incorrect threads on fittings were installed to the case drains of both gearboxes, which almost caused catastrophic failure as both had been leaking because the plugs could not be tightened.
Incorrectly specified pipes
Incorrectly specified pipes were used in the engine room, and the lack of anti siphon breaks was causing continual flooding. One pump failure, or small fire, and the vessel would have sunk.
Sump box
A very small box in the front of the engine room was the dump for the shower, sink, macerator, dishwasher and a couple of drains. There was no seal on the box, the pump was too small, meaning it overflowed into the engine room. The smell in the engine room was overwhelming. fermentated waste was all through the bilges slopping around as the ship moved. Every time a sink flushed or the shower was used it would end up in the bilge.
Aft door construction
In just three months the aft door began to fail. First the coatings fell off as corrosion began. The cause was incorrect and/or nonexistent preparation to the aluminum. Rather than align the components correctly, large “wads” of semi cured fiberglass chop strand were jammed in the corners to make the incorrect fitting work. The entire door had to be re-built.
Seals not filled
Most external fittings on the cruiser were not sealed. This has a catastrophic effect on a vessel, as the ingress of water corrodes, it assists some laminates to fail, and can destroy inner cores, also to fittings and equipment around.
Dry laminate
Investigating further, a small weep was found oozing out of the stem of the vessel. On grinding off the outer gel coat we found the deck to hull joint was not laminated correctly . The inner core was lacking resin enrichment.
Chain run bedding
After removing the winch and with difficulty the chain run and bowsprit the culprit was found. The entire anchoring system had been sat down on handfuls of chopped strand fiberglass, lumps of glue and laminated in this fashion to poorly enriched glass matting.
Nothing had been sealed. Whenever it rained or water came over the bow it ran under the fastenings and then tracked along the deck join which was full of voids. Having nowhere to go it then pushed off the gel coat to ooze out of the hull.
Fairing incompatibility
An incorrect type of fairing had been used everywhere. There was no adhesion to any coating. Obviously, we could not repair the issue as each time we “feathered back” the gel coat more fell off.
At the same time we were repairing the driveline and altering it to align correctly with the stern tubes. In order to do this we had to remove both struts. Both literally fell off.
Great voids were found going deep into the hull laminate. The fastening holes showed us the hull was not a similar thickness, but instead went from a few millimeters, to 15 millimeters. Water had seeped into the core and after three weeks was still dripping out.
Strut alignment
By the time the strut was aligned correctly,the engines had to be raised in the front by an extraordinary 55mm, and the engine by 30mm. Apart from obvious shaft damage caused by the accident, both shafts had their end tapers cut out of concentric, meaning they would never spin true from the start.
Whilst attending to raising the engines, a large burn area was noticed up against the hull and forward bulkhead. Investigation showed the diesel heater had almost set the ship on fire. Incorrect type of insulation had been placed around the exhaust and this had burnt deep into the laminate of the inner hull.
It had got so hot it had destroyed the fire retardant lining on the forward bulkhead. The heater was bolted to the fuel tank with the main feed line passing against the exhaust of the eberspatcher heater. When the heater had been installed, the fastening had been destroyed. Rather than repairing this, a simple “fix” was made by using a standard plastic zip tie to hold everything against the fuel tank securely.
Woodwork delaminating
Lovely timber surrounds around the engine room door and lovely looking timberwork in the inside of the ship had started to spring apart. Incorrect glues had been used.
Then came the biggest shock of all. On core drilling to re- install an incorrectly positioned skin fitting and valve, the core drilled fell apart as the hole saw was withdrawn. After trying a couple of different methods to see if perhaps the “sheer or tear” to the laminate was caused through mechanical coring, we found it was not. The vessel had without been laminated without a careful note of checking resin saturation and without looking at the basic figure of “how much area of cloth versus how much resin used was applied?”
Incorrectly specified inverter
This inverter supplied power to the ship when the ships generators are not in use. While we moved the vessel we had to turn off the shore power and run on the ships batteries until we had completed the move. Ten minutes after the move had started the yacht’s main inverter bank began to smoke and overheat losing all power to the ship.
The warranty for the unit was twelve months from commissioning. It had never been commissioned. After further checks, the battery bank’s capacity was completely incorrect. The unit had failed as no-one had checked how much power on a continual basis it could produce.
The owner had been sold many extra’s such as wine chillers, fans, etc, but apart from selling him all the extras for his boat, the manufacturers failed or ignored a simple important fact of summing up all the energy the cruiser would consume so the energy system would be designed around those requirements. We now had to re-design and build an extensive power system.
The total repair cost was over $250,000.00
on a yacht that had been purchased as brand new
How could this have been avoided?
Building boats is not difficult if the quality standards are followed. But if the standards are not observed during the yacht’s construction, then repairing it is difficult as well as very expensive. Good Project Management will help you avoid costly mistakes.